Non-cylindrical hot air chamber?
Non-cylindrical hot air chamber?
Hello. I am a newbie and this is my first post. Mechanically inclined all my life but not mathematical enough for engineering calculations. I hope my ignorance and ability to misunderstand do not prove frustrating to those kind enough to prove answers and suggestions.
Question 1: Understanding that a displacer is not a compression piston but a low pressure mover of air, is there an inherent design requirement for an air chamber to be cylindrical? Can it be, for example, a cube? (The question goes to materials used in the construction of a large, stationary engine.) The power cylinder and piston would be cylindrical and metal.
Question 2: What defines low temperature and high temperature? At what point in the cycle is that measurement taken? What temperature is considered the threshold of a high temperature engine?
Question 3: I understand the regenerator is not so much a conservation of fuel (which it can be) but a mechanism to increase power production by maximizing temperature deferential. Building this Stirling would have 2 primary ambitions, a large volume water pump *and* to harvest heat to help maintain consistent thermophilic (high temperature) digestion inside biomass digesters producing methane. I assume this heat harvesting would best be done on the cooling end of the air chamber; internal and external closed loop circulating water to cool the internal air and transfer it into the digesters. (Please correct me if I am wrong.) If this collection of heat (thus cooling the cool end) is efficient enough, is it considered a regenerator? Would there be need for or additional benefit from a regenerator within the displacer?
Question 4: To the purpose of #3, I envision dome shapes at each end of the displacer. The domes would push air into corresponding cavities at each end of the air chamber. On the cooling end, displacing heated air through an internal circulating water radiator (possibly a car radiator). On the heating end, the air would be displaced into internal radiant fins or tubing atop the heat source. (Please correct me if there is an obvious flaw in this.)
Thank you for any answers and suggestions. I have already learned so much from weeks of reading previous posts prior to registering.
Question 1: Understanding that a displacer is not a compression piston but a low pressure mover of air, is there an inherent design requirement for an air chamber to be cylindrical? Can it be, for example, a cube? (The question goes to materials used in the construction of a large, stationary engine.) The power cylinder and piston would be cylindrical and metal.
Question 2: What defines low temperature and high temperature? At what point in the cycle is that measurement taken? What temperature is considered the threshold of a high temperature engine?
Question 3: I understand the regenerator is not so much a conservation of fuel (which it can be) but a mechanism to increase power production by maximizing temperature deferential. Building this Stirling would have 2 primary ambitions, a large volume water pump *and* to harvest heat to help maintain consistent thermophilic (high temperature) digestion inside biomass digesters producing methane. I assume this heat harvesting would best be done on the cooling end of the air chamber; internal and external closed loop circulating water to cool the internal air and transfer it into the digesters. (Please correct me if I am wrong.) If this collection of heat (thus cooling the cool end) is efficient enough, is it considered a regenerator? Would there be need for or additional benefit from a regenerator within the displacer?
Question 4: To the purpose of #3, I envision dome shapes at each end of the displacer. The domes would push air into corresponding cavities at each end of the air chamber. On the cooling end, displacing heated air through an internal circulating water radiator (possibly a car radiator). On the heating end, the air would be displaced into internal radiant fins or tubing atop the heat source. (Please correct me if there is an obvious flaw in this.)
Thank you for any answers and suggestions. I have already learned so much from weeks of reading previous posts prior to registering.
Last edited by TomOliver on Wed Jun 22, 2011 10:47 pm, edited 1 time in total.
Re: Non-cylindrical hot air chamber?
Hi TomOliver, engines have been built with square/ rectangular shapes, its just that round seems more conveniant in most cases. I take motors that run on tempereatures from the heat of ones hand, to ones that run on a bowl of boiling water to be low temperature motors. the ones that require a gas(LPG/ Butane/ Propane), or a spirit burner to be high temperature. I suppose the ones that run with a candle would be a medium heat motor. With my motors they are mostly high temp, and the hot end is usually at least a dull red(depending on how well the burner is working), some motors I run at quite a bright red.
Can't help much with the maths, about all I use is to calculate the volume of the cylinders, so that I can work out the ratio between the displacer and the power cylinders, if you can't adjust the volume by the diameter, you alter the stroke.
For cooling I pulled apart a little car heater radiator, and built up my own design. The tubes are flat (3 mm x 10 mm) I cut them 100 mm long, made a top and bottom tank with two rows of 6 slots for the tube ends, and soldered it all together. This works OK as a thermosyphon. The full size heater radiator did'nt work, it would need a pump, and my motors are fairly small. I have used other designs of radiator.
Get books, I use James G. Rizzo's "The Stirling Engine Manual", and last year I built a Ross Yoke type motor, so when Andy Ross made his book available, free on line, I got hold of that. Ian S C
Can't help much with the maths, about all I use is to calculate the volume of the cylinders, so that I can work out the ratio between the displacer and the power cylinders, if you can't adjust the volume by the diameter, you alter the stroke.
For cooling I pulled apart a little car heater radiator, and built up my own design. The tubes are flat (3 mm x 10 mm) I cut them 100 mm long, made a top and bottom tank with two rows of 6 slots for the tube ends, and soldered it all together. This works OK as a thermosyphon. The full size heater radiator did'nt work, it would need a pump, and my motors are fairly small. I have used other designs of radiator.
Get books, I use James G. Rizzo's "The Stirling Engine Manual", and last year I built a Ross Yoke type motor, so when Andy Ross made his book available, free on line, I got hold of that. Ian S C
Re: Non-cylindrical hot air chamber?
A pleasure to meet you, Ian SC. I have enjoyed reading and already absorded quite a bit from other contributions you have made to the forum. I especially enjoyed the machinist dislogues you had with a couple other forum members attempting to Stirling a heavy V airpump. Admired the ingenuity... cleaning bearing and shaving grams.
I am reading Andy Ross now and have the other you recommended but won't start on that until I have studied the very practical Mr. Ross.
Shape of the air chamber is a key issue for us. If we build, the engine will be stationary, adjacent to well and cistern, making mass irrelevent. Metal is scarce, expensive and difficult to transport into our remote region of East Africa. Square or rectangular being acceptable, we can build a chamber from locally quarried and shaped stone (a skilled handcraft here) and make it airtight using ceramic-crete. Based on magnesium oxide and phosphorus mixed with polymers (a recipe developed for encapsuling of radioactive wastes), the cerami-crete would be sufficiently airtight, absolutely moisture proof, withstand up to 1,600 psi compression and a sustained temp of 1,800F. I doubt our primitive walking beam could ever reach that psi or temp.
The same ceramic-crete might form our hollow displacer; similar to how ferrocement uses steel rods and wire mesh to form shapes, this substance is lighter than Portland, uses lightweight fabric for form and requires only 10-12mm that can be sprayed or paintbrushed. Expensive stuff, but not in the volume we require. (FYI, this stuff is being used now in Haiti to provide shelters. Soak a tent in a slurry of it, put up the tent, cut window opening if desired, and an hour later you have a permanent, waterproof, cerami-crete shelter.)
The power cylinder and piston would be more convention, cylindrical and metal.
We are still at the feasibility research, hope to progress to design and then fabrication, but it will be a slow go. Thanks for helping us with a first step.
I am reading Andy Ross now and have the other you recommended but won't start on that until I have studied the very practical Mr. Ross.
Shape of the air chamber is a key issue for us. If we build, the engine will be stationary, adjacent to well and cistern, making mass irrelevent. Metal is scarce, expensive and difficult to transport into our remote region of East Africa. Square or rectangular being acceptable, we can build a chamber from locally quarried and shaped stone (a skilled handcraft here) and make it airtight using ceramic-crete. Based on magnesium oxide and phosphorus mixed with polymers (a recipe developed for encapsuling of radioactive wastes), the cerami-crete would be sufficiently airtight, absolutely moisture proof, withstand up to 1,600 psi compression and a sustained temp of 1,800F. I doubt our primitive walking beam could ever reach that psi or temp.
The same ceramic-crete might form our hollow displacer; similar to how ferrocement uses steel rods and wire mesh to form shapes, this substance is lighter than Portland, uses lightweight fabric for form and requires only 10-12mm that can be sprayed or paintbrushed. Expensive stuff, but not in the volume we require. (FYI, this stuff is being used now in Haiti to provide shelters. Soak a tent in a slurry of it, put up the tent, cut window opening if desired, and an hour later you have a permanent, waterproof, cerami-crete shelter.)
The power cylinder and piston would be more convention, cylindrical and metal.
We are still at the feasibility research, hope to progress to design and then fabrication, but it will be a slow go. Thanks for helping us with a first step.
Last edited by TomOliver on Thu Jun 23, 2011 7:23 am, edited 1 time in total.
Re: Non-cylindrical hot air chamber?
TomOliver
The regenerator is not simply a chiller, the function of the regenerator is to capture the warmth of the hot gas, and return it to the gas, when, cooled, goes back to the heated part. The regenerator must be made of very thin metal so that the metal temperature change rapidly (so the exchange is rapid, shares better with different temperatures, in both directions), ...a chiller works in one direction only.
Ferraccio
The regenerator is not simply a chiller, the function of the regenerator is to capture the warmth of the hot gas, and return it to the gas, when, cooled, goes back to the heated part. The regenerator must be made of very thin metal so that the metal temperature change rapidly (so the exchange is rapid, shares better with different temperatures, in both directions), ...a chiller works in one direction only.
Ferraccio
Re: Non-cylindrical hot air chamber?
Ah, thank you. Importance noted.
That prompts a theoretical (and I have observed in my reading how well versed you are in the formulas): Should we be concerned about extracting too much heat on the cooling side, reducing the overall temp too much and reducing output? I doubt we could be that efficient even if we wanted to, but is it a valid consideration? We anticipate that initially our heat source will be a wood burning rocket mass heater with stout steel fins or many conductive tubes (surface area) built into the bottom of the (airtight) air chamber atop the heat source. Woodgas is also an option.
Another question, please. I am sure I will come to these in the books I am reading, but your input would help me to understand it better: Is it necessary for the displacer to actually displace by volume? Is it sufficient if the displacer simply shifts air from one end to the other (sort of a low compression piston). Example, a relatively thin plane with perpendicular aluminum tubes packed with coolant such as steelwool or copperfiber thru which the air passes with slight resistance?
That prompts a theoretical (and I have observed in my reading how well versed you are in the formulas): Should we be concerned about extracting too much heat on the cooling side, reducing the overall temp too much and reducing output? I doubt we could be that efficient even if we wanted to, but is it a valid consideration? We anticipate that initially our heat source will be a wood burning rocket mass heater with stout steel fins or many conductive tubes (surface area) built into the bottom of the (airtight) air chamber atop the heat source. Woodgas is also an option.
Another question, please. I am sure I will come to these in the books I am reading, but your input would help me to understand it better: Is it necessary for the displacer to actually displace by volume? Is it sufficient if the displacer simply shifts air from one end to the other (sort of a low compression piston). Example, a relatively thin plane with perpendicular aluminum tubes packed with coolant such as steelwool or copperfiber thru which the air passes with slight resistance?
Re: Non-cylindrical hot air chamber?
Meanwhile, I hope I have understood your question, I know very little English:
The Stirling engine works (like all other heat engines) on the temperature difference.
So more the engine is warm from the hot side and the more cold from the cold side, greater may be the amount of energy that can be extracted.
Certainly, however, a refrigeration system that extracts heat too well that is NOT introduced, at least ... it's useless, (and even dangerous, see below).
I said that MAY be extracted, it is not like that either, to do that is you need to build a good engine.
One way to do a good engine is doing well three elements: the heater, the regenerator, the cooler.
Then there are two physical-mechanical factors: the mechanical build well (seals, frictions) and especially to MEASURE the dead space; for sealing and frictions I hope you know what it means, for the dead space: the dead space volumes are those where the fluid is "unnecessarily", that is where it goes or stays, or do not get a heat exchange or work.
The dead spaces are deadly to stifle the flow of energy that allows the extraction of work. Please note that the Stirling cycle the gas is a closed volume.
And THIS also makes unnecessary spaces to broach the subject of the cooler.
One more thing that is often overlooked, as there is in the hot side and cold side, must ensure that the heat does not pass through the metal between them, but only through the gas in motion.
Thus a diaphragm seal between the two metal parts, ie porcelain between the two sides can be useful.
Ciao, Ferraccio
The Stirling engine works (like all other heat engines) on the temperature difference.
So more the engine is warm from the hot side and the more cold from the cold side, greater may be the amount of energy that can be extracted.
Certainly, however, a refrigeration system that extracts heat too well that is NOT introduced, at least ... it's useless, (and even dangerous, see below).
I said that MAY be extracted, it is not like that either, to do that is you need to build a good engine.
One way to do a good engine is doing well three elements: the heater, the regenerator, the cooler.
Then there are two physical-mechanical factors: the mechanical build well (seals, frictions) and especially to MEASURE the dead space; for sealing and frictions I hope you know what it means, for the dead space: the dead space volumes are those where the fluid is "unnecessarily", that is where it goes or stays, or do not get a heat exchange or work.
The dead spaces are deadly to stifle the flow of energy that allows the extraction of work. Please note that the Stirling cycle the gas is a closed volume.
And THIS also makes unnecessary spaces to broach the subject of the cooler.
One more thing that is often overlooked, as there is in the hot side and cold side, must ensure that the heat does not pass through the metal between them, but only through the gas in motion.
Thus a diaphragm seal between the two metal parts, ie porcelain between the two sides can be useful.
Ciao, Ferraccio
Re: Non-cylindrical hot air chamber?
About the displacer:
all architectures need absolutely a LONG displacer; this becouse all the gas contained have to be moved, BUT ALSO IS NECESSARY THAT THE HOT WALL DO NOT CHILL COMING IN CONTACT TO COLD GAS (IE THE ONE UNDER A "DIAPHRAGM" DISPLACER ....BY YOU PROPOSED), for the same meaning the displacer should have LOW MASS, LOW THERMAL CONDUCTION AND LOW THERMAL CONTENT.
Time ago I proposed very thin porcelain for the displacer, if are accomplished, for very thin walls, sufficient mechanical performances in phisical condition that they are.
The ceramic materials, if are hy tech, are expensive, and the use however should be allowable only in hy tech engines.
For standard is commonly used very thin (light mass) stainless plate, that, as metal, have good mechanical performances, quite low thermal conduction, and quite low thermal content. And ..... the low mass is also important being the displacer have to be moved....
Ferraccio
all architectures need absolutely a LONG displacer; this becouse all the gas contained have to be moved, BUT ALSO IS NECESSARY THAT THE HOT WALL DO NOT CHILL COMING IN CONTACT TO COLD GAS (IE THE ONE UNDER A "DIAPHRAGM" DISPLACER ....BY YOU PROPOSED), for the same meaning the displacer should have LOW MASS, LOW THERMAL CONDUCTION AND LOW THERMAL CONTENT.
Time ago I proposed very thin porcelain for the displacer, if are accomplished, for very thin walls, sufficient mechanical performances in phisical condition that they are.
The ceramic materials, if are hy tech, are expensive, and the use however should be allowable only in hy tech engines.
For standard is commonly used very thin (light mass) stainless plate, that, as metal, have good mechanical performances, quite low thermal conduction, and quite low thermal content. And ..... the low mass is also important being the displacer have to be moved....
Ferraccio
Re: Non-cylindrical hot air chamber?
The recomended proportions for the displacer; the length should be about 3 x the diameter, and the volume about i.5 times the power cylinder. thats the basic maths required for a high temp hot air engine. And it is best to keep the stroke of the crank fairly short.
My best displacer cylinders are made of thin, .5 mm stainless steel, as is the displacer its self. Some displacers are mild steel, and three of the cylinders are also. There are 15 motors in my collection at the moment. Ian S C
My best displacer cylinders are made of thin, .5 mm stainless steel, as is the displacer its self. Some displacers are mild steel, and three of the cylinders are also. There are 15 motors in my collection at the moment. Ian S C
Re: Non-cylindrical hot air chamber?
About materials: is important that you collect
- tables of thermal conduction
- tables of thermal expansion
- data of hot bearing
Aluminium has very good thermal conduction (204) when carbon steel is approx 55-60. Aluminium has a huge thermal expansion (24) when carbon steel is 12.
Stainless steel (normal) have less thermal conduction (22-25) than carbon steel. The thermal expansion is (approx) similar to carbon steel.
Aluminium however do not bears well temperatures more than 300 °C, for so is not adapt to hot if temperatures may be go over.
Standard carbon steel do not bear well for long time high temperatures, (oxidation and lowering of mechanichal caracteristics) also if having to find a good "low alloy carbon steel" (Cr, Ni, Mo, W), (normally used for good level machinery) you may have good performances.
Nickel and and its no-iron alloy, are good, but are many expensive, and useful only in high tech, or at last for regenerator (small mass in thin foils).
Mechanical coupling aluminium-steel, is good only to bear, if they are exigence of sealing have to use o-rings (thermal expansions are different).
In syntesis: stainless steel is useful and for many uses, aluminium is very good for not heated parts, being is very light in weigh.
- tables of thermal conduction
- tables of thermal expansion
- data of hot bearing
Aluminium has very good thermal conduction (204) when carbon steel is approx 55-60. Aluminium has a huge thermal expansion (24) when carbon steel is 12.
Stainless steel (normal) have less thermal conduction (22-25) than carbon steel. The thermal expansion is (approx) similar to carbon steel.
Aluminium however do not bears well temperatures more than 300 °C, for so is not adapt to hot if temperatures may be go over.
Standard carbon steel do not bear well for long time high temperatures, (oxidation and lowering of mechanichal caracteristics) also if having to find a good "low alloy carbon steel" (Cr, Ni, Mo, W), (normally used for good level machinery) you may have good performances.
Nickel and and its no-iron alloy, are good, but are many expensive, and useful only in high tech, or at last for regenerator (small mass in thin foils).
Mechanical coupling aluminium-steel, is good only to bear, if they are exigence of sealing have to use o-rings (thermal expansions are different).
In syntesis: stainless steel is useful and for many uses, aluminium is very good for not heated parts, being is very light in weigh.
Re: Non-cylindrical hot air chamber?
The length of the displacer is influenced by many other factors in the design. I high temp engine needs a long displacer because of the distance the air (or other gas) must travel to reach the other end of the engine. A low temperature differential engine can have a very short displacer, as you see in many "pancake" style engines. (The MM-5 displacer is only about 1/8" thick.) And there are some older designs that just have two pistons and no displacer. So the answer to that question depends on the other design parameters of your engine. It needs to fit your design, move the air between the heating and cooling areas, and not contribute to any thermal shorting or dead space.
My LTD designs use a square pressure chamber with a vertically oriented displacer that is only 1/4" thick. That particular arrangement works very well in an LTD design, but I don't think I have seen anyone try to make a power producing engine with that configuration.
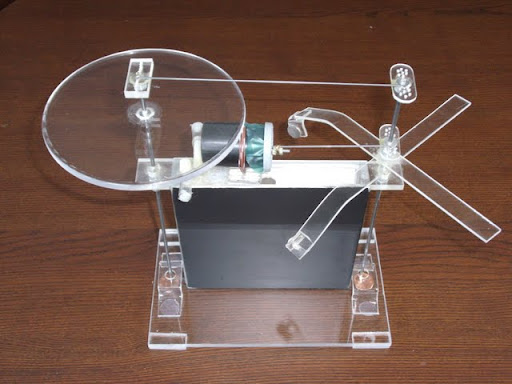
My LTD designs use a square pressure chamber with a vertically oriented displacer that is only 1/4" thick. That particular arrangement works very well in an LTD design, but I don't think I have seen anyone try to make a power producing engine with that configuration.
Last edited by jimlarsen on Sun Jun 26, 2011 8:50 pm, edited 1 time in total.
Jim Larsen
http://StirlingBuilder.com
http://StirlingBuilder.com
Re: Non-cylindrical hot air chamber?
Thank you, Mr. Larsen for helping to put displacer shape, size and stroke into perspective. I have enjoyed visiting your website often and learned from it before joining here. A pleasure to meet you. It is you and other miniature builders who have preserved and refined the Stirling concept thru the decades of petroleum internal combustion, and now the pendulum (or walking beam) might be swinging back toward the solar and wind and Stirling.
Mr. Ferraccio has made some valuable comments concerning thermal properties of various materials and their placement within the engine, and emphasized the importance of regeneration. We are now collecting data on which refractory and insulative materials we can harvest and refine locally (such as the kaolin necessary for good ceramic to become good porcelain) and beginning to toy with placement of those materials within the walls of an air chamber and the shell of the displacer.
To put my displacer size/shape focus in context, what we are considering might be the world's largest ;) - and likely most primitive - Stirling.
While our area is preciously short of refined metals, we have a great diversity of raw minerals. From this the area has a heritage of skilled stone masons and potters using locally harvested materials. This project began with the need to construct a new and much larger (walk-in size) kiln of naturally available materials, and consideration of how to fuel it the airtight kiln to the high temps required for hours at a time and the temperature regulation needed to produce fine ceramics and porcelains.
Then while viewing a YouTube of a miniature walking beam Stirling, a concept hit me: Put a walking beam on top, a displacer shaft down the chimney and a power cylinder thru one wall and our kiln becomes giant Stirling. (That is both exaggeration and simplification, but is the genesis of this project.) It will not happen that way, too impossibly big... lol, but I can foresee scaling down to a large, relatively low rpm/high torque Stirling (much of it built of ceramic materials, rather than metal ) sitting atop a kiln and being fueled by the heat from the kiln.
In good business and permaculture, we try go get as many evironmentally and economically feasible uses from each thing we do. Firing of kiln fuels Stirling that pumps water and provides heat to biogesters that generate methane to fuel a commercial size community electrical generator.
Thank you for your contribution.
Mr. Ferraccio has made some valuable comments concerning thermal properties of various materials and their placement within the engine, and emphasized the importance of regeneration. We are now collecting data on which refractory and insulative materials we can harvest and refine locally (such as the kaolin necessary for good ceramic to become good porcelain) and beginning to toy with placement of those materials within the walls of an air chamber and the shell of the displacer.
To put my displacer size/shape focus in context, what we are considering might be the world's largest ;) - and likely most primitive - Stirling.
While our area is preciously short of refined metals, we have a great diversity of raw minerals. From this the area has a heritage of skilled stone masons and potters using locally harvested materials. This project began with the need to construct a new and much larger (walk-in size) kiln of naturally available materials, and consideration of how to fuel it the airtight kiln to the high temps required for hours at a time and the temperature regulation needed to produce fine ceramics and porcelains.
Then while viewing a YouTube of a miniature walking beam Stirling, a concept hit me: Put a walking beam on top, a displacer shaft down the chimney and a power cylinder thru one wall and our kiln becomes giant Stirling. (That is both exaggeration and simplification, but is the genesis of this project.) It will not happen that way, too impossibly big... lol, but I can foresee scaling down to a large, relatively low rpm/high torque Stirling (much of it built of ceramic materials, rather than metal ) sitting atop a kiln and being fueled by the heat from the kiln.
In good business and permaculture, we try go get as many evironmentally and economically feasible uses from each thing we do. Firing of kiln fuels Stirling that pumps water and provides heat to biogesters that generate methane to fuel a commercial size community electrical generator.
Thank you for your contribution.
Re: Non-cylindrical hot air chamber?
Just a note, there is a vidio on line some where of a hot air motor (? in Germany), with an oil drum for a displacer. Ian S C
Re: Non-cylindrical hot air chamber?
Perhaps you are referring to the prototype of the Stirling Technologies engine? 5hp engine it hopes to put into mass production. http://cdn3.wn.com/vp/i/2f/2d63ae191678b7.jpg
I am still too early in the reading/learning process to be talking design, but I am playing with displacer ideas:
At the bottom of the displacer, a bell/bowl/parabola. Line the bowl surface with thin metal - stainless stell or brass. Suspend inside the bell a metal honeycomb to maximize surface area *within* the bowl.
Between that bowl and where it attaches to the main body of the displacer, a conduction heat barrier backed by an insulating material.
Above that, the hollow, insulated, lightweight main body of the displacer.
The thinking is:
At maximum bottom stroke for the bell cavity to trap air in the space between the bell and the heat source. Concentrate the initial heating within that space. Heat that air as much as possible with the least possible heating of the displacer and air chamber walls. As the displacer rises, might the bell shape draft displaced air into the Hot Spot bell honeycomb?
Have my amateur design speculations made a fool of me yet?
That's ok, I do not have an ego problem and am not easily discouraged.
Hahaha! This is fun, an old dog trying to learn new tricks.
I am still too early in the reading/learning process to be talking design, but I am playing with displacer ideas:
At the bottom of the displacer, a bell/bowl/parabola. Line the bowl surface with thin metal - stainless stell or brass. Suspend inside the bell a metal honeycomb to maximize surface area *within* the bowl.
Between that bowl and where it attaches to the main body of the displacer, a conduction heat barrier backed by an insulating material.
Above that, the hollow, insulated, lightweight main body of the displacer.
The thinking is:
At maximum bottom stroke for the bell cavity to trap air in the space between the bell and the heat source. Concentrate the initial heating within that space. Heat that air as much as possible with the least possible heating of the displacer and air chamber walls. As the displacer rises, might the bell shape draft displaced air into the Hot Spot bell honeycomb?
Have my amateur design speculations made a fool of me yet?

Hahaha! This is fun, an old dog trying to learn new tricks.
Last edited by TomOliver on Sun Jun 26, 2011 3:36 pm, edited 1 time in total.
Re: Non-cylindrical hot air chamber?
Hy Tom,
Well I also think I'm an old dog that looks.
with regard to technology, I think your doing a nice mix of high technology, and doing things yourself.
Honeycomb structure ...and find the kaolin to make porcelain.
There are standard porcelain caolin, and special powder of porcelain, compounds of silicate, that can leak cold as pasta, and are then cooked to 105 degrees Celsius (only) for one hour.
Are thermally insulating, can be machined (turned, drilled, threaded and grinded), holds up to over 1000 degrees Celsius, have a limited withdrawal, resist thermal shock, good mechanical characteristics, and obviously they are light in weight.
There is also an "ultra light solid silicate foam", I think it's similar to the tiles that isolated the belly of the Space Shuttle.
I worked today to amend the heading "steam car" (Italian wikipedia), particularly for existing steam engines, modern.
All high-tech steam engines have pistons, cylinders and also ceramic bearings, all strictly non-lubricated or water-lubricated (oil lubrication is impossible in a steam engine)
See: "Cyclone engine" in Net.
I really smile reading your "Mr. Ferraccio" Ferraccio is my nickname, and means.. "Very bad Iron .."
Ciao, F
Well I also think I'm an old dog that looks.
with regard to technology, I think your doing a nice mix of high technology, and doing things yourself.
Honeycomb structure ...and find the kaolin to make porcelain.
There are standard porcelain caolin, and special powder of porcelain, compounds of silicate, that can leak cold as pasta, and are then cooked to 105 degrees Celsius (only) for one hour.
Are thermally insulating, can be machined (turned, drilled, threaded and grinded), holds up to over 1000 degrees Celsius, have a limited withdrawal, resist thermal shock, good mechanical characteristics, and obviously they are light in weight.
There is also an "ultra light solid silicate foam", I think it's similar to the tiles that isolated the belly of the Space Shuttle.
I worked today to amend the heading "steam car" (Italian wikipedia), particularly for existing steam engines, modern.
All high-tech steam engines have pistons, cylinders and also ceramic bearings, all strictly non-lubricated or water-lubricated (oil lubrication is impossible in a steam engine)
See: "Cyclone engine" in Net.
I really smile reading your "Mr. Ferraccio" Ferraccio is my nickname, and means.. "Very bad Iron .."
Ciao, F