I just stuck the piston back in as-is and gave it a whirl.
There was actually improved performance. All 20 LED's lit up nice and bright.

- Resize_20230515_193215_5750.jpg (92.49 KiB) Viewed 9623 times
The voltage under load was just 2 volts
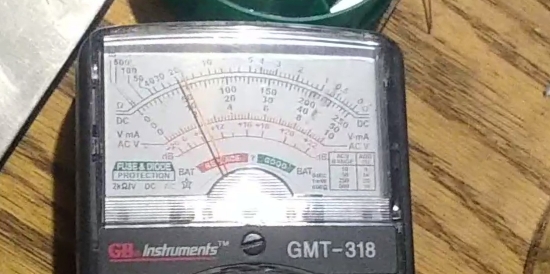
- Resize_20230515_192744_4149.jpg (111.6 KiB) Viewed 9623 times
Unfortunately, or fortunately, this time the engine really blew out (or burned out) a seal by the time I was done recording, (not yet uploaded) and some smoke can be seen billowing out the side of the engine through the blown seals when turning the engine over by hand, after it quit running completely.
I only managed to hold the volt meter to the generator contacts for a couple seconds, fumbling around with propane torch, two meter probes and the phone, but, the 2 volts while under load is definite, as I was able to get a better reading with two hands while not recording.
I haven't measured the voltage output no-load as yet.
The engine, however, is out of commission and will need a rebuild, so that will have to wait.
Just as well. I think I've done all the preliminary testing I needed to do, if for no other reason, to convince myself there is any reason to pursue this further.
Really it was VincentG's successes with working with this type of engine that got me inspired to try it again after sitting on the shelf for the past ten years.
Thanks VincentG !