The pans are almost a perfect fit for the glass displacer cylinder I cut out of a bottle with an inner dia of appr 3 3/8". There's maybe 1mm play, mostly due to the bottle's non-uniform diameter. A bit of RTV and there should be no problems with air leakage. The pans seem strong enough for a LTD, pressing on the center when upside down gives no bend without substantial force, but this may be more to do with the form than the thickness.
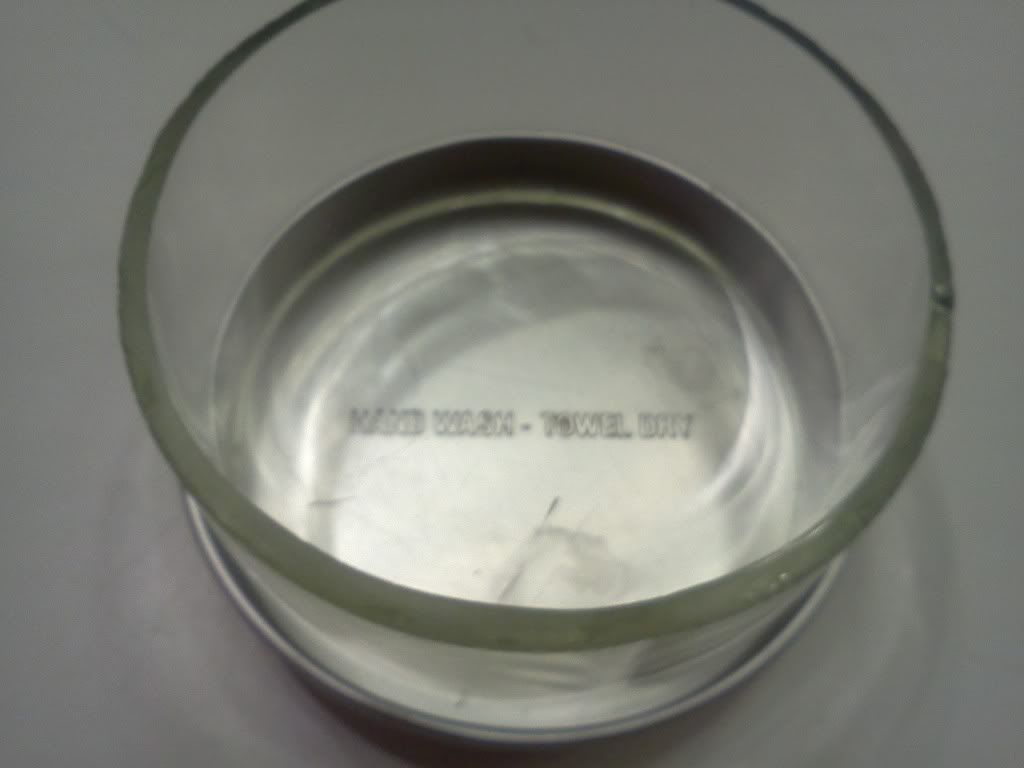
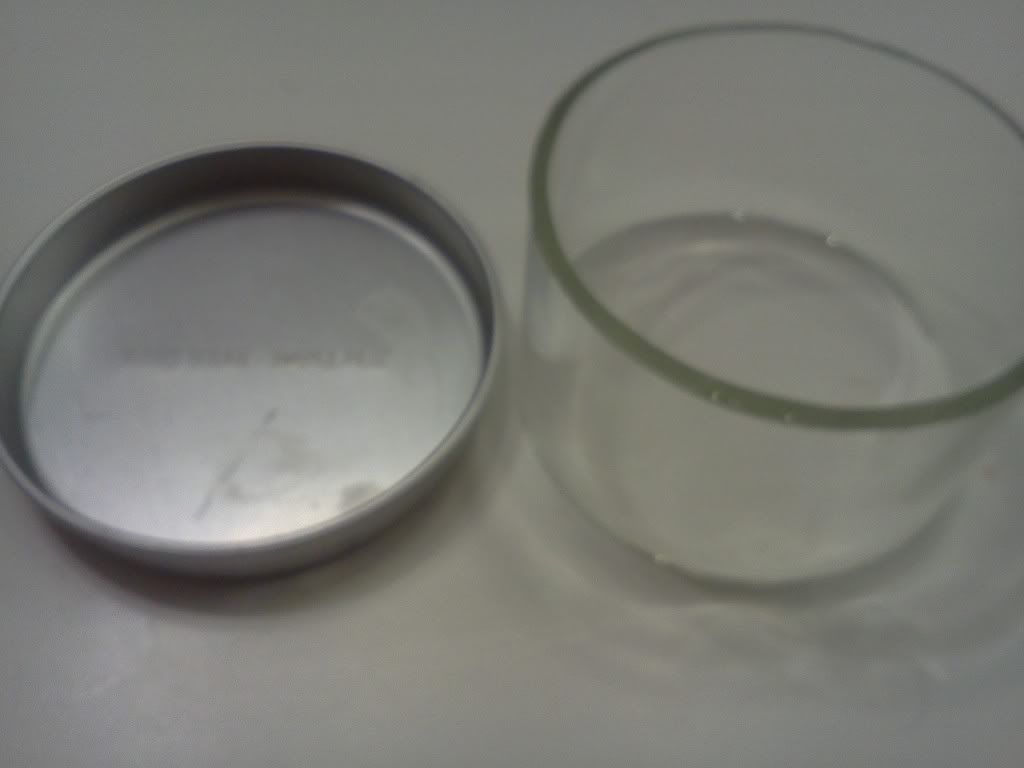
This will be set into a cutout of the stainless steel hot box, with an appropriate mating gasket to prevent the posibility of bi-metal corrosion.
I cut the brass top plate today as well, decided to go square (might go octoganal) due to my lack of a lathe and lack of practice with a grinder for cutting. The existing holes are perfectly placed for the sign posts, so I measured to make use of them in my cutting. Don't know what the gauge of the brass sheet is, but it measures about 1/32", so it's not easy to work with hand tools, but I'm getting decent results. I'm actually kinda proud of my cut, seeing as how I did it free hand letting the cutting disc (grinder) work as the guide once my cut was started, then deburred with the dremel. Lots of cleanup and polishing to look forward to!
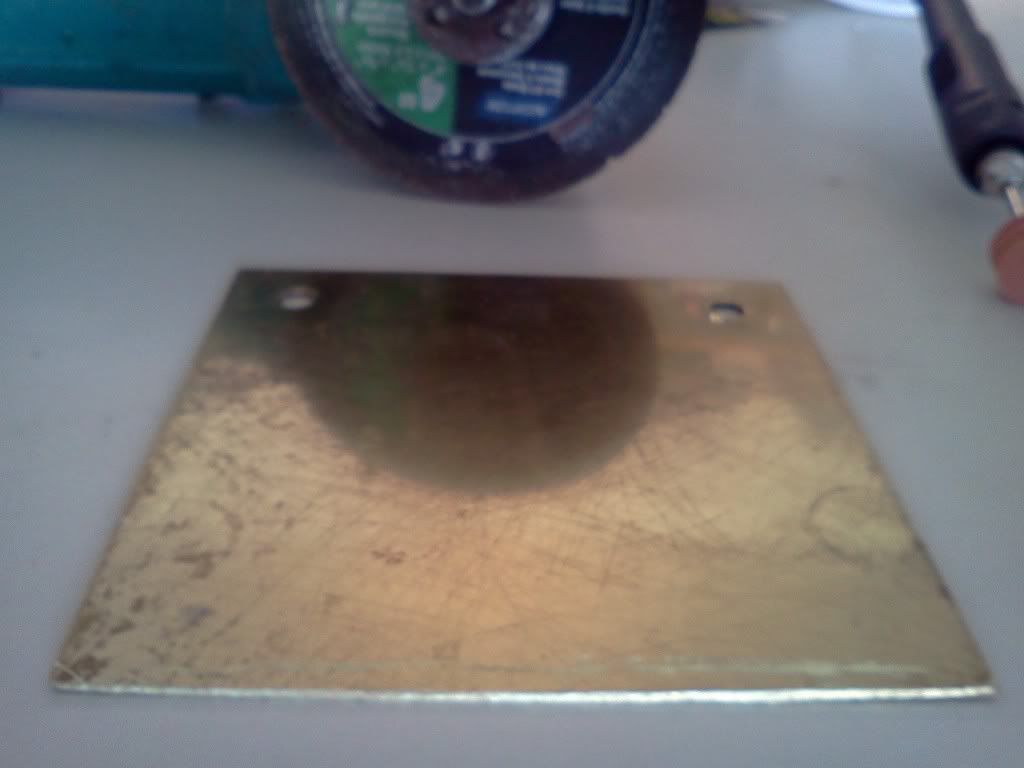
All of you with access to shop tools, I truly envy you right now. I spent 2 hours wet sanding the displacer tubes, and I've still got probably another 2 hours to go before I'll be happy with it (spreading the tedious jobs out over days helps keep me from getting frustrated). With a belt sander it would have taken me 5 minutes. While I'm happy with my brass sheet cut, it's not perfect, and you do see a bit of light when placed on a flat surface, but it looks good to the naked eye.