Had an old pair of rubber work boots in the garage I haven't used in years, cut the top of one off to make a gasket the same height as the aluminum pan in the hot box, minus it's tiny flange height. Ground out the circle I cut out till the pan and gasket are a tight press fit without deforming the gasket. It fully covers the sides of the aluminum pan below the flange, may trim it to expose more of the pan if necessary for better heat transfer. I used scissors to cut the rubber boot, which left a couple of small miscuts in the rubber, may redo it with a razor and straight edge, but I'm very happy with the results so far.
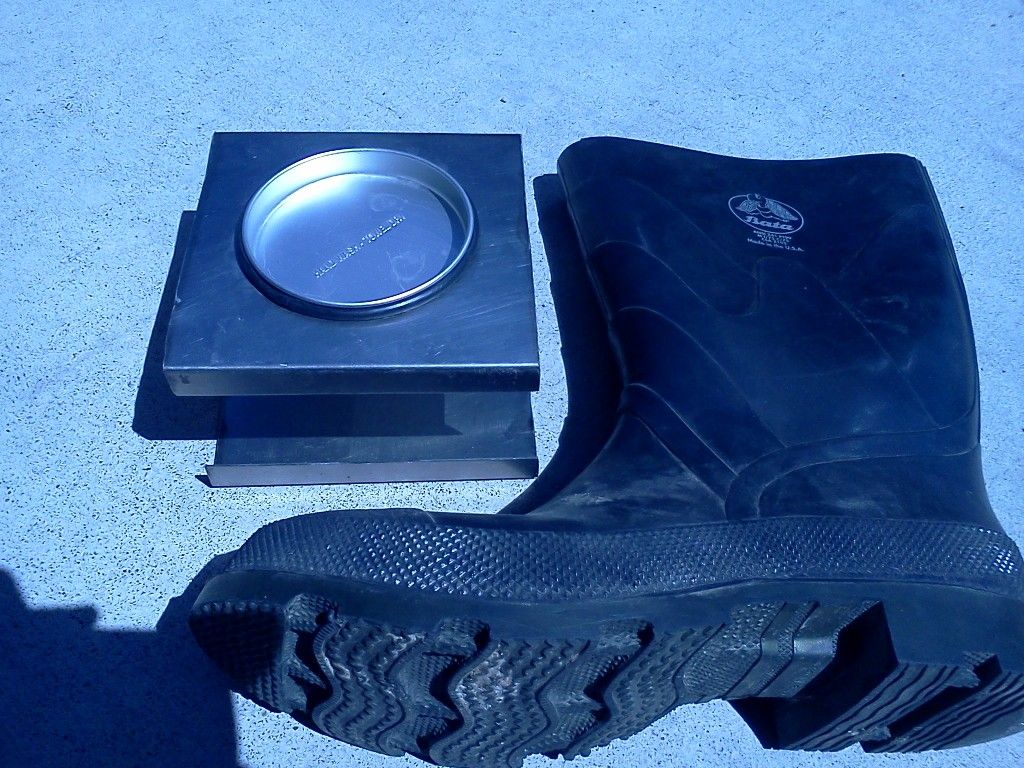
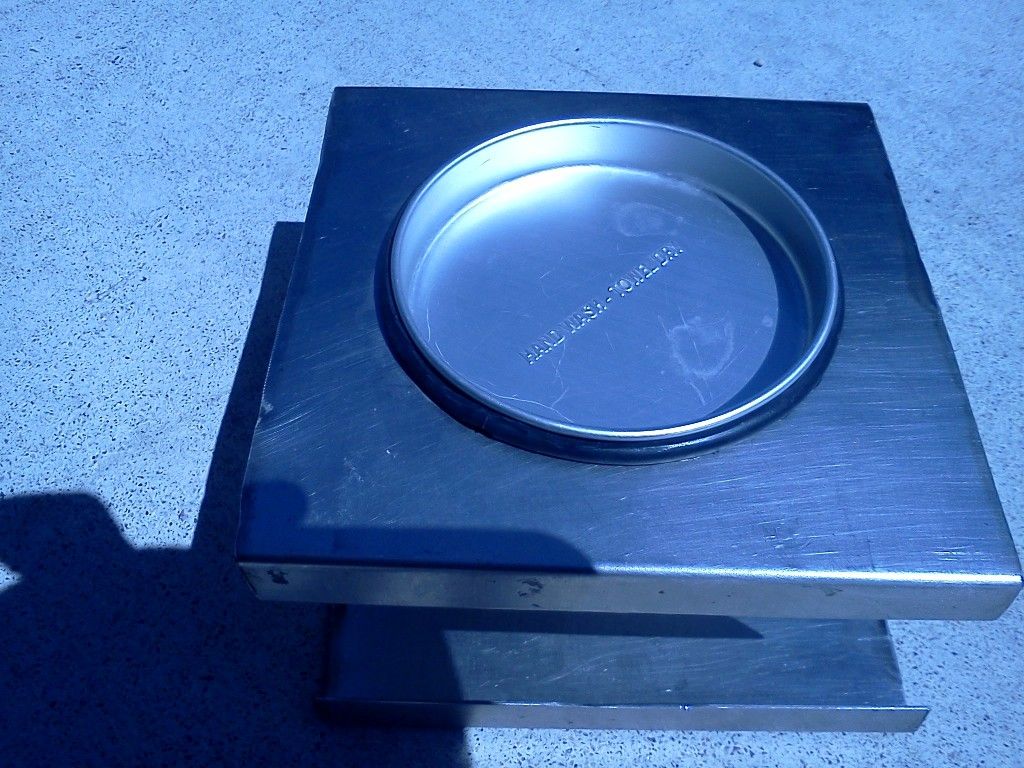
I measured out and drilled the holes for the crankstands, displacer shaft, and power cylinder. I made the rear crankstand hole larger than necessary to allow some positioning before tightening down. I've discovered the rear crankstand was sucked into the bearing housing more than the front one during curing by a bit over 1/16". Will have to use a washer or o-ring to increase it's height a smidge, dang quick set epoxy. Was going to assemble the crankshaft and do the first rough assembly today, but I need to get some brass laquer. I only have wood laquer around the house, and brass laquer will prevent tarnishing longer, especially important on my stoned finish. I first did the stone finish a couple of weeks ago, and it's already showing tarnish, so good laquer is a must.
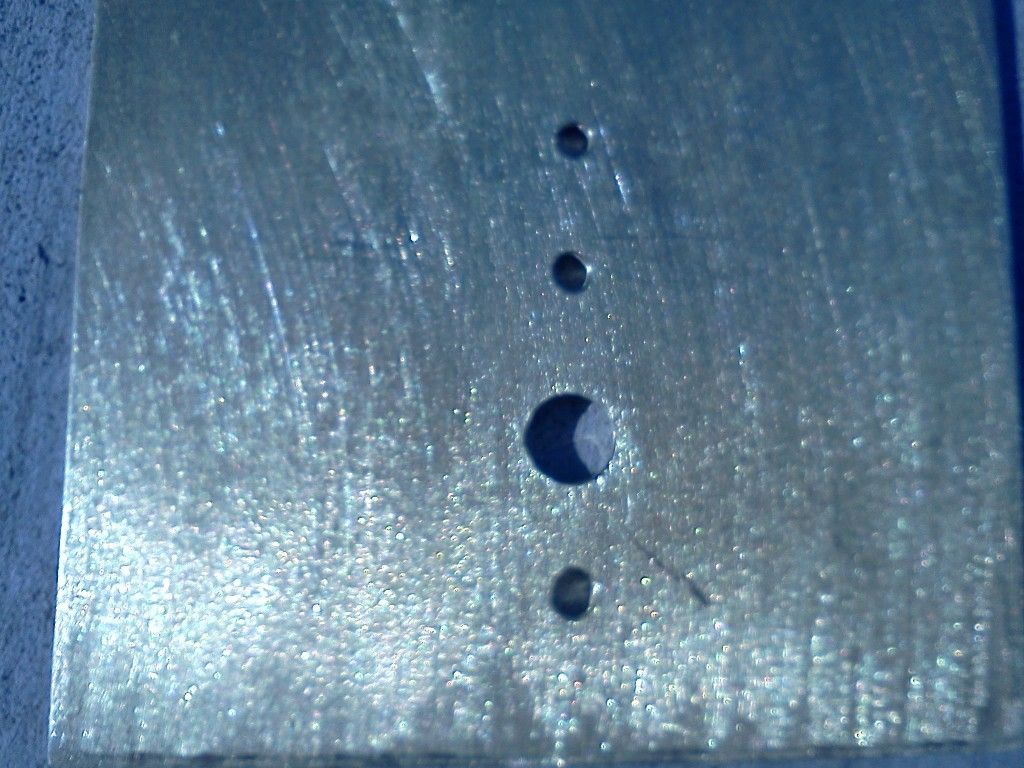